14 Types of Clothing Printing Techniques
- Xinyue Qiu
- Feb 5, 2024
- 5 min read
Updated: Aug 3, 2024
The scope of printing techniques in clothing is vast, so here I will select the most practical types, simplifying the complexity, and providing practical examples to illustrate. Knowing this, you can experiment with combining different printing techniques and fabrics, as they will produce various effects. It’s quite interesting. Let's get started!
1.Transfer Printing
This common printing technique involves applying pigments to paper to create a transfer print, which is then transferred to fabric using heat and pressure. Transfer printing is straightforward, requires minimal investment, and is widely used in the market.
This method is typically used for synthetic fabrics and is known for producing vibrant colors, detailed layers, realistic patterns, and strong artistic appeal. However, it is mostly suitable for certain synthetic fibers like polyester.
2. Digital Direct Printing
This method is commonly used for printing on silk and cotton fabrics. It involves using reactive dyes that chemically bond with the fibers during the dyeing process. It is mainly applied to fabrics like pure cotton, pure linen, silk, and other woven or knitted materials with a high content of these fibers.
Comparison: Heat Transfer vs. Printing Digital Printing
Heat Transfer Printing:
Best for 100% polyester fabrics, providing vibrant results.
When mixed with cotton, it may cause white spots or a messy appearance.
There are transfer papers for cotton, but they may result in prints that deteriorate after washing.
Digital Printing:
Ideal for cotton fabrics, especially T-shirts.
Offers a softer feel as the ink permeates the fabric without a glue-like texture.
Generally more expensive than heat transfer printing.
Choosing the Right Method:
For jerseys or quick-drying clothes, choose heat transfer printing.
For cotton T-shirts, opt for digital direct printing.
In summary, the choice depends on the fabric type and desired performance. Digital printing provides a softer feel and better results on cotton but at a higher cost. Heat transfer is more affordable and best for polyester, but it may have durability issues on cotton.
3. Screen printing
Screen printing uses a mesh screen to transfer ink onto a surface. The process begins by preparing a fine mesh screen stretched over a frame. The design is transferred onto the screen using a light-sensitive emulsion, leaving open areas where ink can pass through while the rest is blocked.
Ink is spread over the screen, and a squeegee presses the ink through the mesh onto the substrate below. This process can be repeated with different screens and colors for multi-colored designs.
Screen printing is known for its vibrant colors and durability, making it ideal for textiles, paper, plastics, and more. However, it may not be suitable for highly detailed designs due to limitations in mesh size and resolution.
4. Discharge Printing

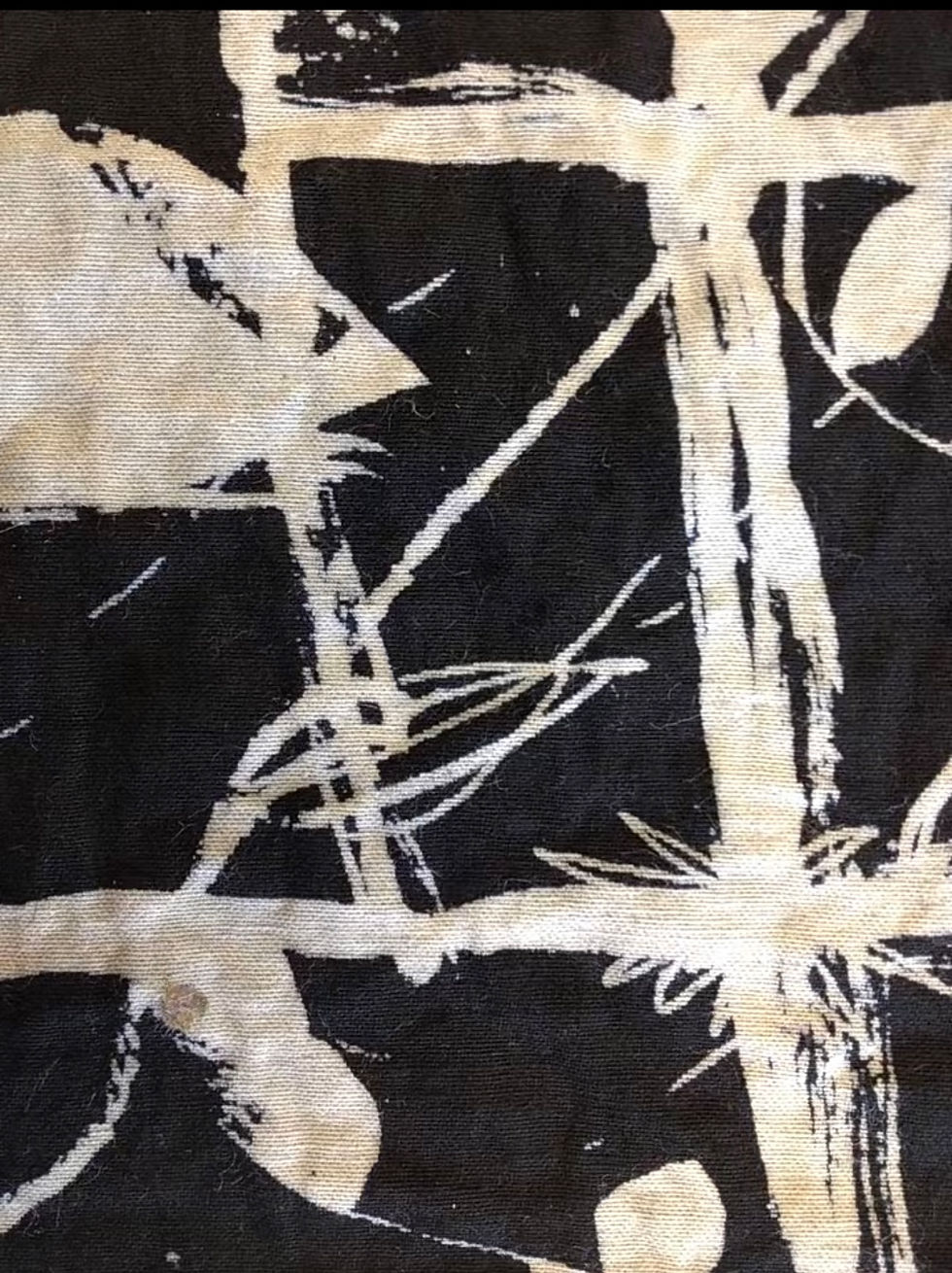
This method removes the fabric's color to create a washed-out effect. The garment appears mottled and faded because the process removes the dye from the fabric's fibers, giving it a lighter, washed look—this creates a unique and cool effect.
Discharge printing involves dyeing the fabric with a color that lacks discharge resistance. After drying, a printing paste containing a discharge agent is applied. During the post-treatment, the dye in the printed areas is destroyed and faded, forming white patterns or colored patterns from the resistant dye.
5. Reducing Printing
Also known as burnout printing, this technique takes advantage of the different chemical resistance properties of fibers in blended fabrics. By applying a corrosive agent, one fiber type is locally removed, leaving behind the other to create semi-transparent patterns.
6. Crinkle Printing

Also known as embossed printing, this technique involves applying chemicals to fabric, causing fibers to expand or contract. This creates a contrast between the printed and non-printed areas, resulting in regularly embossed patterns on the surface, like bubble gauze printed with caustic soda.
7. Water Slurry Printing
Water slurry is a widely used, water-based paste for printing. It offers a soft feel and is best suited for light-colored fabrics due to its weak coverage.
This method is cost-effective, but it has a major limitation: the slurry is lighter than the fabric, making it ineffective for darker fabrics. Consequently, water slurry is only suitable for printing light colors on dark backgrounds, not the other way around. While it doesn’t achieve high color saturation like high-end watermarks, it preserves the fabric's original texture and breathability, making it ideal for large-area prints.
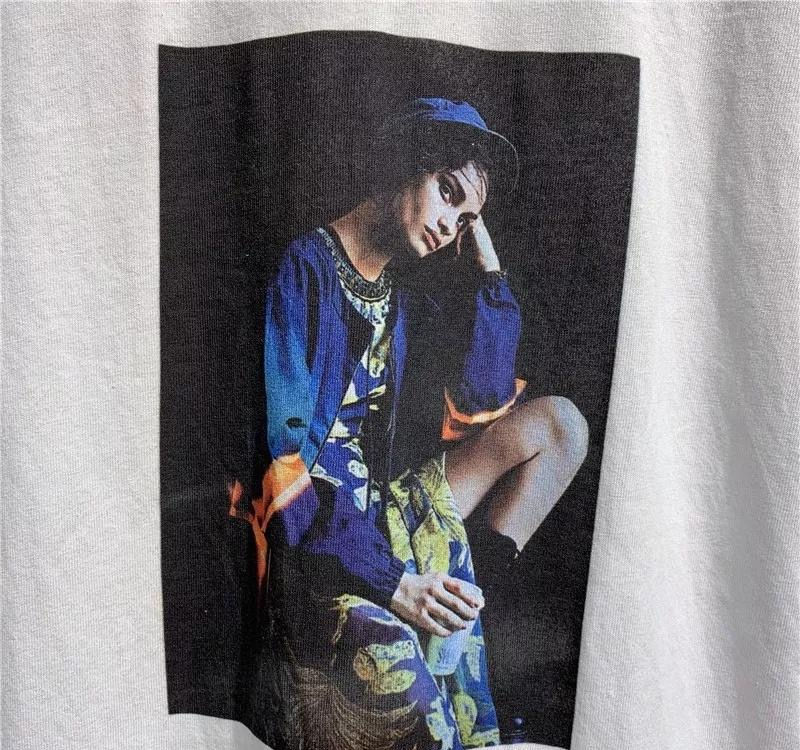
8. Gel Printing

Gel printing, widely adopted after water slurry, is known for its excellent coverage and ability to print light colors on dark fabrics. It adds a glossy, three-dimensional effect, making garments look upscale. This method has become popular for T-shirts.
However, gel printing can be stiff, making it unsuitable for large, solid patterns. For better results, use water slurry for large areas and add gel for detail to reduce stiffness and enhance pattern depth. Alternatively, creating a sparse pattern with a "distressed" effect can also address the stiffness issue, though it might still feel hard to wear.
Gel printing comes in glossy and matte finishes and offers softness, thinness, and environmental benefits. Both gel and water slurry prints are washable. Price-wise, gel printing is more cost-effective than water slurry.
9.Foam Printing
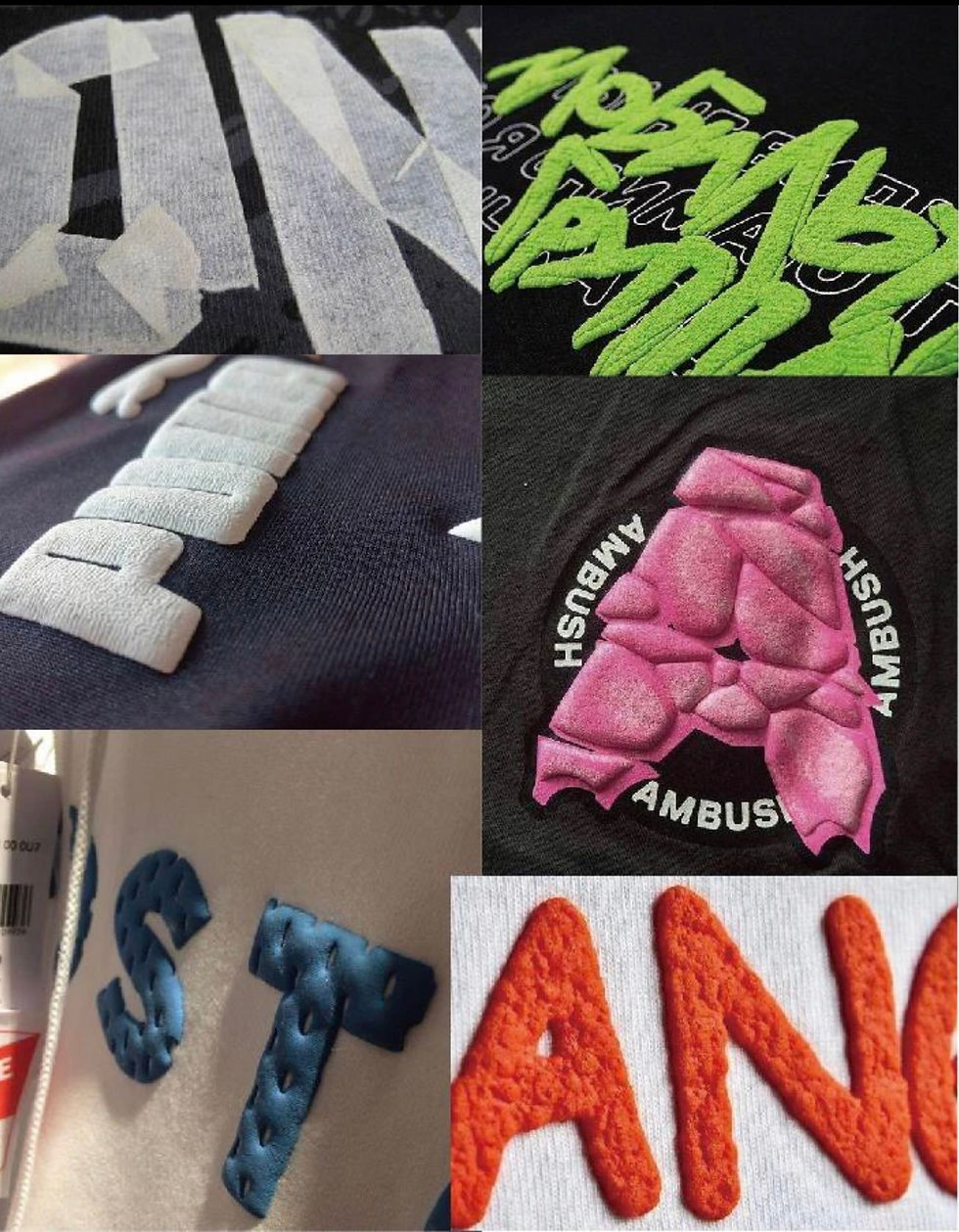
Foam printing uses a slurry that expands into foam. Derived from gel printing, the process involves applying the slurry to fabric and then using a high-temperature machine to create a raised, foam-like pattern. This technique provides a good three-dimensional effect and a soft feel. However, with repeated wear and washing, the raised effect tends to flatten over time.
10. Drip Glue
Drip glue creates a more three-dimensional effect than thick plate printing. It's commonly used for making drip glue patches, especially in men's wear. In women's wear, it's often used for decorative patterns, while in men's wear, it's applied to entire designs.
The main drawback is that it can break off if subjected to excessive force. Currently, drip glue is most commonly used in accessories like webbing.
11. Ink Printing
At first glance, ink printing might seem similar to gel printing, but it has a key advantage: it adheres better to smooth fabrics like trench coat materials. Unlike gel, which can be easily scraped off, ink printing offers superior color fastness.
Ink printing is ideal for trench coats, providing bright colors and vivid, lifelike images. It was popular for "head printing" a few years ago, known for producing extremely clear and hyper-realistic prints.
You can also add gold or silver powder to the ink for extra dimension. Typically, the cost of ink printing depends on the number of colors used, with more colors increasing the price.
12. Velvet Printing

In simple terms, velvet printing is a technique used to apply short-fiber fluff to fabric surfaces in specific patterns. It is designed specifically for creating a velvety texture and is not used for other materials or fabrics.
13. Gold Stamping & Silver Stamping
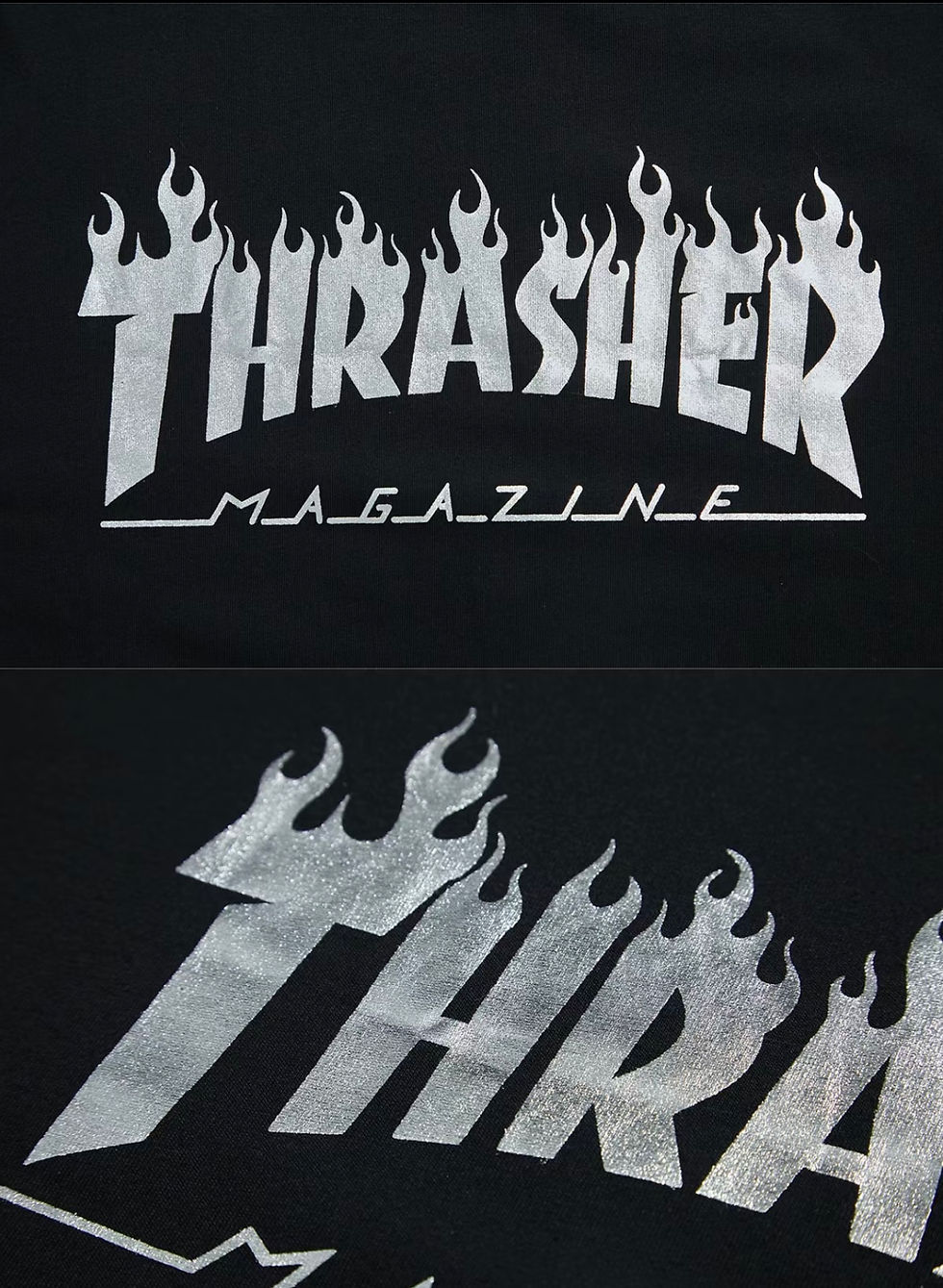
Simply put, gold stamping involves pre-making a pattern on a plate (usually concave), applying glue to the plate, and then transferring gold color from gold stamping paper to the fabric according to the plate’s shape. This technique is commonly used in sporty casual styles and typically features patterns like numbers, letters, geometric shapes, or lines, which should not be too thin.
14. Crackling

Contains special ingredients that shrink and harden when heated. When screen-printed onto T-shirt fabric and allowed to dry naturally, it creates a distinctive cracked texture reminiscent of a tortoise shell.
This technique can be combined with various printing methods and is versatile enough for different patterns.
In conclusion:
Patterns today are expressed in diverse and creative ways. Designers frequently mix various printing techniques, and often blend printing with embroidery and other special methods previously discussed. This combination of printing, embroidery, and unique techniques allows for rich, multidimensional designs.
Exploring patterns is exciting due to its limitless possibilities!
Cool!